Get uniform results with skilled plastic extrusion techniques
Get uniform results with skilled plastic extrusion techniques
Blog Article
Understanding the Basics and Applications of Plastic Extrusion in Modern Manufacturing
In the world of contemporary production, the method of plastic extrusion plays a critical function - plastic extrusion. This complex process, including the melting and shaping of plastic through specialized passes away, is leveraged across different sectors for the creation of diverse products. From auto components to durable goods packaging, the applications are huge, and the potential for sustainability is similarly outstanding. Untangling the principles of this process exposes the true convenience and capacity of plastic extrusion.
The Principles of Plastic Extrusion Process
While it might appear facility, the basics of the plastic extrusion procedure are based on fairly uncomplicated concepts. It is a production process where plastic is thawed and after that shaped into a continual account through a die. The plastic extrusion procedure is extensively made use of in different markets due to its cost-effectiveness, efficiency, and flexibility.
Various Kinds of Plastic Extrusion Techniques
Structure upon the fundamental understanding of the plastic extrusion procedure, it is required to explore the various strategies involved in this production method. In contrast, sheet extrusion produces huge, level sheets of plastic, which are generally further processed into items such as food packaging, shower curtains, and car components. Understanding these techniques is essential to making use of plastic extrusion properly in modern-day manufacturing.
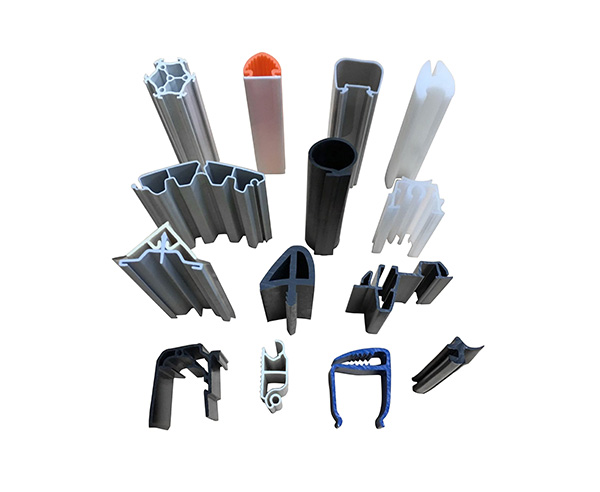
The Function of Plastic Extrusion in the Automotive Sector
An overwhelming majority of parts in modern-day vehicles are products of the plastic extrusion procedure. This process has transformed the auto industry, transforming it right into a much more reliable, economical, and flexible manufacturing industry. Plastic extrusion is primarily made use of in the manufacturing of various automobile elements such as bumpers, grills, door panels, and control panel trim. The process offers an attire, constant result, allowing manufacturers to create high-volume components with excellent precision and marginal waste. The lightness of the extruded plastic parts contributes to the overall reduction in vehicle weight, enhancing fuel performance. Furthermore, the longevity and resistance of these components to warmth, chilly, and influence boost the durability of autos. Thus, plastic more tips here extrusion plays a critical function in vehicle manufacturing.

Applications of Plastic Extrusion in Consumer Item Manufacturing
Past its substantial effect on the auto market, plastic extrusion shows just as effective in the realm of consumer items making. This procedure is crucial in developing a wide variety of products, from food packaging to family home appliances, toys, and even clinical gadgets. The adaptability of plastic extrusion allows makers to design and generate intricate sizes and shapes with high precision and efficiency. Furthermore, as a result of the recyclability of many plastics, extruded parts can be reprocessed, decreasing waste and cost. The adaptability, flexibility, and cost-effectiveness of plastic extrusion make it a favored selection for numerous customer goods makers, contributing significantly to the market's development and innovation. The environmental implications of this extensive use need careful factor to consider, a topic to be discussed even more in the succeeding area.
Ecological Effect and Sustainability in Plastic Extrusion
The prevalent usage of plastic extrusion in producing invites scrutiny of its eco-friendly implications. Reliable equipment reduces energy use, while waste monitoring systems recycle scrap plastic, reducing raw material needs. Despite official site these renovations, even more advancement is needed to mitigate the ecological footprint of plastic extrusion.
Conclusion
In verdict, plastic extrusion plays a critical duty in modern manufacturing, especially in the automotive and durable goods industries. Its adaptability enables the production of a vast array of components with high accuracy. Moreover, its possibility for reusing and development of biodegradable products provides a promising opportunity in the direction see here now of sustainable practices, therefore addressing environmental worries. Comprehending the fundamentals of this process is vital to enhancing its applications and benefits.

The plastic extrusion procedure is extensively used in numerous markets due to its adaptability, cost-effectiveness, and effectiveness.
Structure upon the standard understanding of the plastic extrusion process, it is essential to discover the various techniques entailed in this manufacturing approach. plastic extrusion. In contrast, sheet extrusion produces big, flat sheets of plastic, which are normally additional refined right into products such as food packaging, shower drapes, and car parts.An overwhelming bulk of components in modern lorries are products of the plastic extrusion procedure
Report this page